
The next step is to export the flat pattern as a DXF or DWG. Save as window highlighting an options button to direct you to the DXF export options. Access this option from the Save As window by hitting the Options… button as shown below.Įxport section of the system options highlighting the custom mapping section. Then, you need to select Export in the left column and click the Enable checkbox under Custom Map SOLIDWORKS to DXF/DWG as seen in the image below. You can access the System Options from the gear icon at the top of the SOLIDWORKS screen. To customize or Custom Map SOLIDWORKS to DXF/DWG, you need to turn a System Option on. For more information on creating and using sheet metal parts in SOLIDWORKS, our Hawk Ridge Systems training class provides all the answers.įeature tree of the sheet metal part displaying the sheet metal folder and sketch in the top level of the tree.

This can be confirmed when you have the Sheet-Metal folder in the Feature Tree as seen below. In order to format bend lines, you must ensure the part file is a sheet metal part.
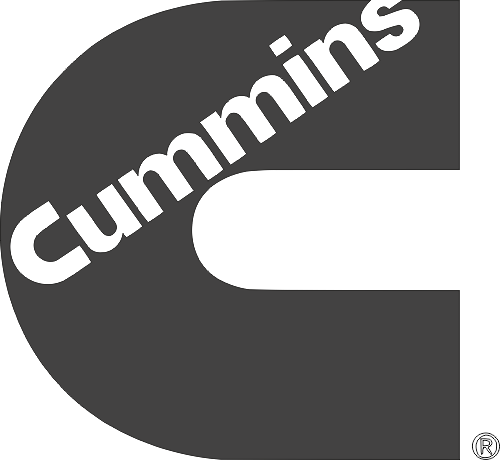
As you can see below, the hawk sketch is always visible and is not being used to generate a feature. In order to format the hawk to be engraved, the sketch containing the hawk must be a top-level feature in the FeatureManager Design Tree and not consumed by a feature. SOLIDWORKS sheet metal model to be used to generate a DXF with custom mapping. The hawk is going to be engraved, the bend lines will be etched, and the model geometry will be cut. Sheet Metal Part Exampleįor this example, I want to create a DXF for this sheet metal part seen below where the model edges, hawk and bend lines all have different formatting. You have the flexibility to change the line style and color for a variety of SOLIDWORKS entities. SOLIDWORKS gives you the option to map different entities (model edges, bend lines, sketches, form tools, etc.) to the required DXF or DWG formatting. Each machine is unique and likes the file formatted in a certain way to distinguish between operations like cutting, engraving, or etching. This should give you exactly what we need without any extra lines.A DXF or DWG file is the common input required for cutting machines like a laser, plasma, hot wire, or water jet cutters. Double-check that everything looks right, click save, and you’re all set!
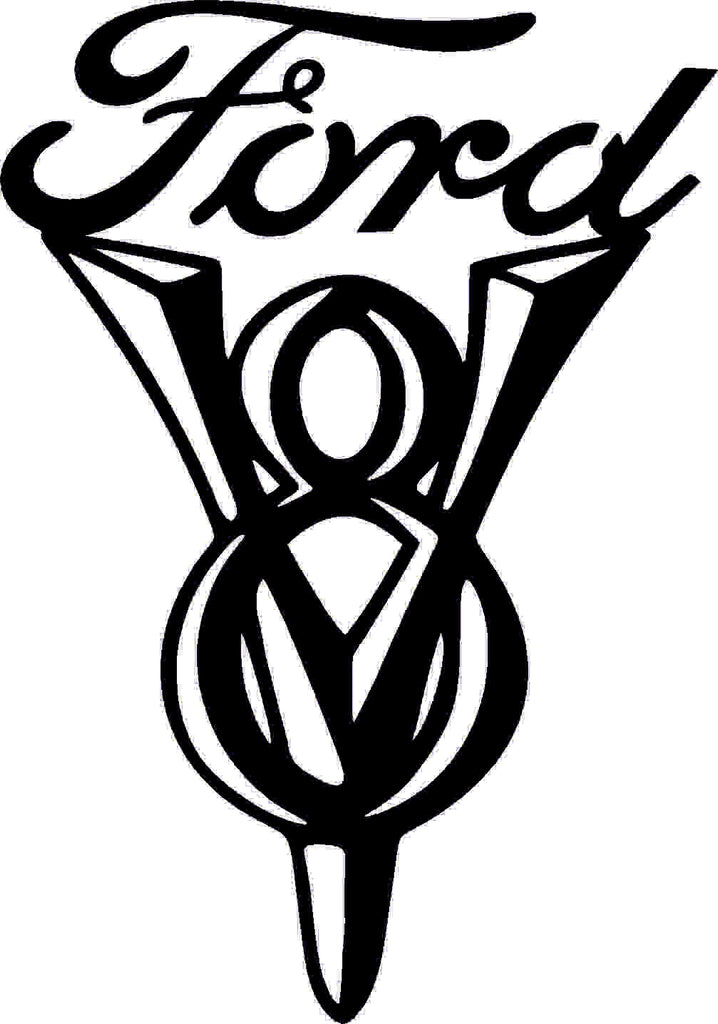
If that looks right, click the green check mark. We just need the top-down “outline” view, exactly as you want the laser to cut it. Confirm that only the face of the part is selected, not the whole body. Select “Export to DXF/DWG.”Ī save dialogue will pop up name your part and select “DXF” as the suffix. When you’re in “Feature” mode looking at the part, right click on the face of the part. Let’s begin!įirst, check your export setting and make sure they look like this:Įxporting all splines and splines will be ideal. But never fear! You can export the outlined face of the part exactly as it should cut by following this tutorial. DXF will flatten all the outlines for the whole part and complicate the cut.
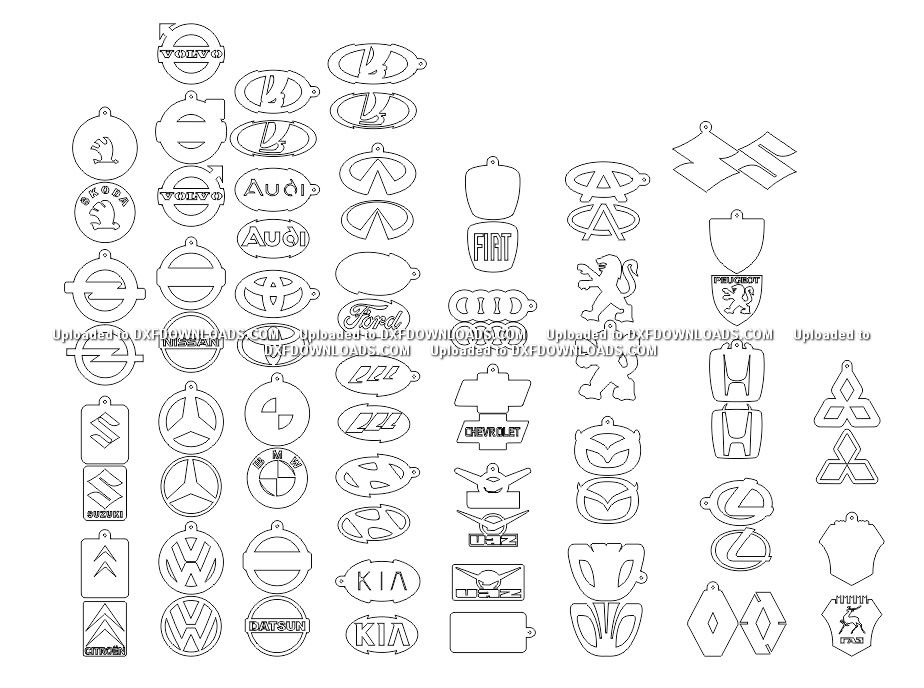
DXF SAMPLE LOGO SOFTWARE
SolidWorks is a preferred modeling software for 3D designs, but we need 2D vector files to cut your parts.
